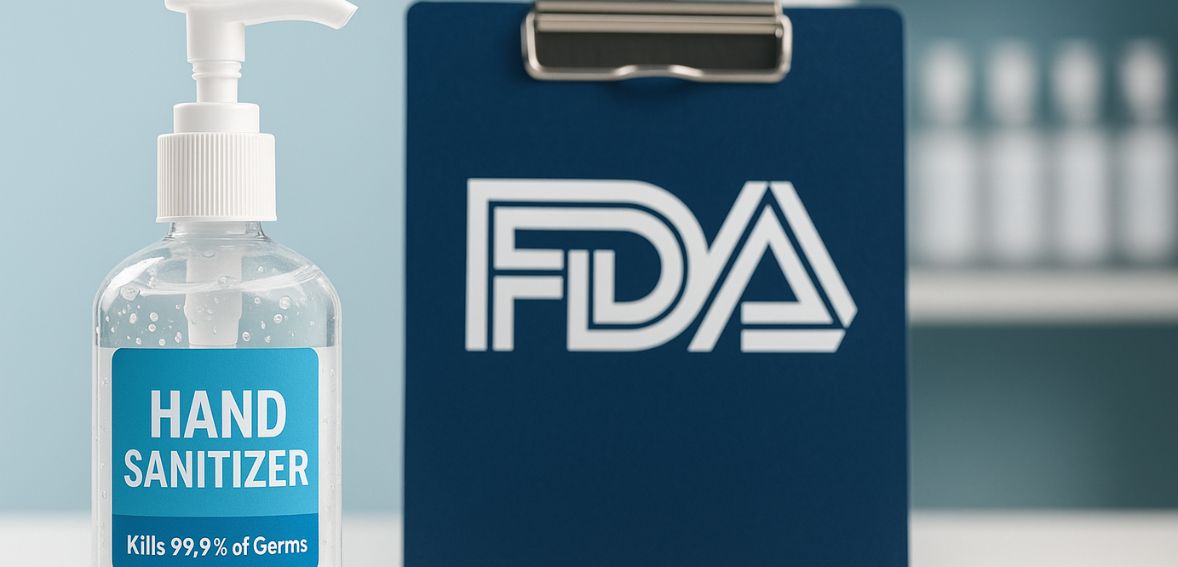
By myhandsanitizershop July 1, 2025
Hand sanitizers are now staple products in homes, workplaces, and public areas in a time when health and cleanliness are more important than ever. However, the U.S. Food and Drug Administration (FDA) enforces a complex set of regulations that extend far beyond the convenience of that small bottle. Manufacturers, distributors, retailers, and even regular consumers who wish to make educated decisions must be aware of these regulations.
By 2025, the FDA’s hand sanitizer regulations have changed dramatically from the early stages of the COVID-19 pandemic, with a renewed focus on consumer safety, supply chain transparency, formulation integrity, and accurate labeling. Even though many of the 2020 emergency relaxations have since been phased out, a few significant developments still have an impact on hand sanitizer production and consumption.
Today’s guidelines reflect a deeper understanding of sanitizer safety, from addressing the risks of inferior ingredients to guaranteeing capacity resilience for future public health emergencies. Not only are hand sanitizers anti-germ products, but they are also over-the-counter (OTC) drug products, which means they have to be produced with strict quality standards and adhere to stringent safety monitoring, labeling, and distribution regulations.
This article provides a comprehensive review of the FDA’s hand sanitizer regulations for 2025. Readers can better understand what it takes to make safe, dependable, and effective hand sanitizers in today’s market by studying formulation standards, quality control procedures, compliance requirements, and consumer advice. These tips will keep you confident in your sanitizer selections, whether you’re a consumer looking for reliable products or a business owner navigating regulatory pathways.
Hand Sanitizer as an Over-the-Counter Drug Product
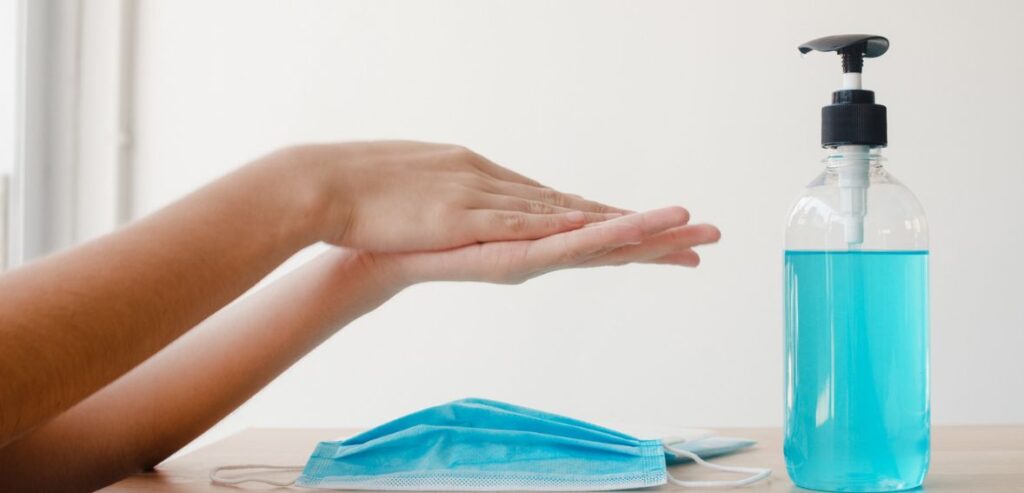
In contrast to many personal care products, hand sanitizers that make claims of disease prevention, such as “killing 99.9% of germs,” are categorized by the FDA as over-the-counter (OTC) drug products. Because of this classification, they are subject to the same regulations as topical creams or Ibuprofen, which means they have to adhere to FDA-approved formulations, good manufacturing practices (GMPs), and labeling specifications.
Manufacturers of new formulations are required to obtain FDA approval or adhere to a final FDA OTC Monograph order requirements. The FDA’s 2019 Hand Sanitizer Drug Monograph outlines permissible manufacturing processes, inactive ingredients, and active ingredients (ethyl alcohol between 60% and 95% and isopropyl alcohol between 70% and 91.3%).
The FDA emphasized strong evidence supporting both safety and efficacy claims in 2025 and clarified that deviations from this monograph require an Abbreviated New Drug Application (ANDA) or full New Drug Application (NDA).
Formulation Standards and Ingredient Integrity
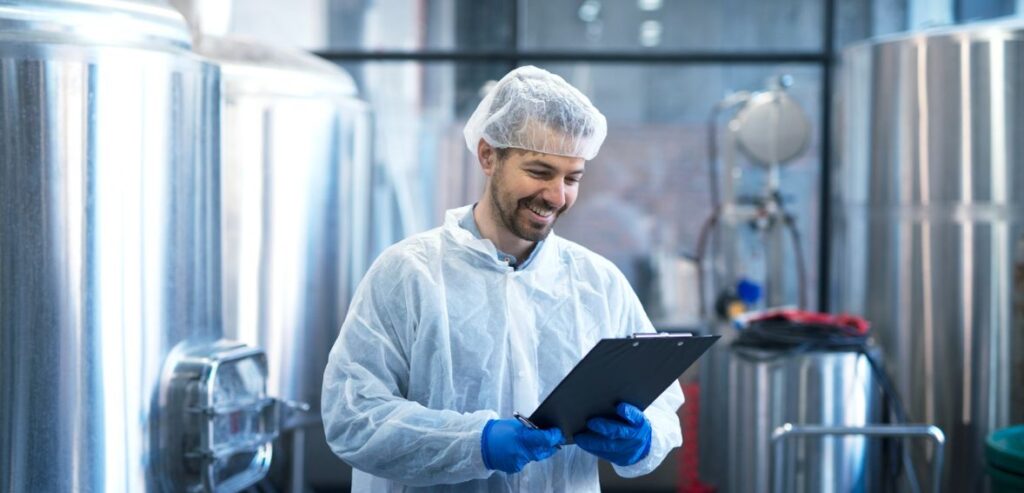
The FDA demands that active and inactive ingredients be precisely specified to guarantee safety and performance. The only active antimicrobials that are currently approved are ethyl and isopropyl alcohol. When used properly, alcohol, water, humectants like glycerin, and mild thickeners make up a suitable arsenal.
The FDA now places a strong emphasis on confirming that alcohol is at least 99% pure and that colorants, solvents, and denaturants adhere to USP (United States Pharmacopeia) or comparable standards. In 2025, avoiding harmful contaminants like methanol, acetaldehyde, and benzene will receive more attention. Past incidents tied to sanitizer recall risks have revealed how poor quality control can lead to dangerous contaminant levels, including methanol.
To make sure ethanol doesn’t contain methanol or other hazardous organic contaminants, the FDA now advises high-sensitivity chemical screenings and recurring batch testing. To ensure traceability and compliance, one particularly crucial step is to demand certificates of analysis (CoA) from ingredient suppliers.
Good Manufacturing Practices (GMPs) and Facility Oversight
The FDA has prioritized stricter GMP enforcement since 2021, mandating that hand sanitizer manufacturers maintain controlled environments akin to pharmaceutical production lines. Standard Operating Procedures (SOPs) must be documented, equipment and processes must be validated, facilities are now required to implement robust cleanliness protocols, while staff must undergo ongoing training to ensure compliance.
GMP enforcement in 2025 entails stricter regulations on equipment sterilization and maintenance, mandatory environmental monitoring for microbes and particulates in production areas, and comprehensive validation of crucial processes—like alcohol concentration testing at final fill. Manufacturers are encouraged to adopt risk-based quality approaches, such as Hazard Analysis Critical Control Points (HACCP). Records of batch production and testing outcomes must be kept for a minimum of three years, or longer if mandated by the contract or application type.
FDA Inspections, Enforcement Actions, and Post-Market Surveillance
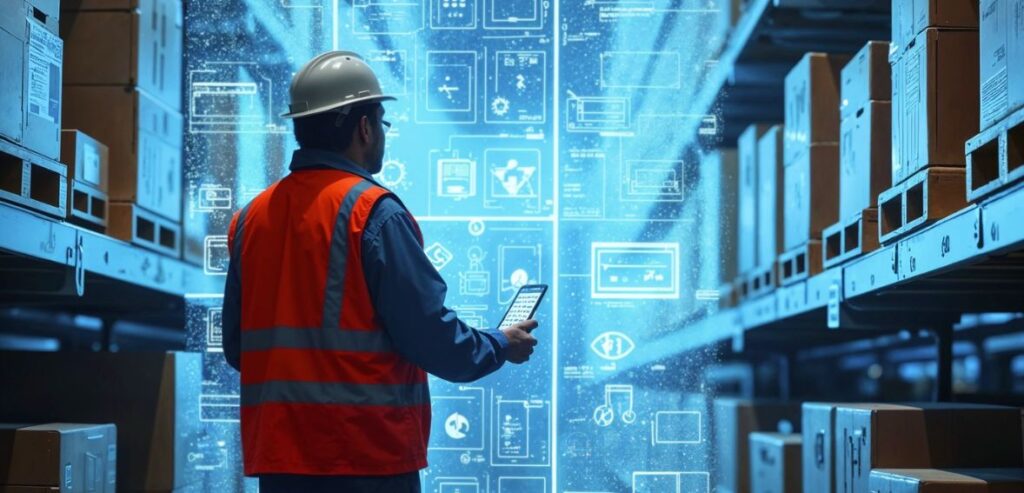
Since 2022, the FDA has resumed regular on-site inspections, which now include surprise visits and follow-ups to previous warning letters. Facility compliance, labeling reviews, batch production records, and raw material sourcing documentation are all covered by inspections. Warning letters, import alerts, product seizures, or recalls are all possible outcomes for noncompliant operations.
To prevent dangerous imports from entering American ports, the FDA collaborates closely with Customs and Border Protection. The agency also runs a post-market surveillance program that gathers data on outbreaks connected to sanitizer use, customer complaints, and adverse event reports.
This monitoring is more robust in 2025, with rapid-response teams prepared to issue recalls or alerts if multiple adverse reactions occur, such as methanol poisoning or skin burns. Additionally, the agency supports consumers’ and healthcare providers’ voluntary reporting.
Labeling Accuracy, Marketing Claims, and Transparency
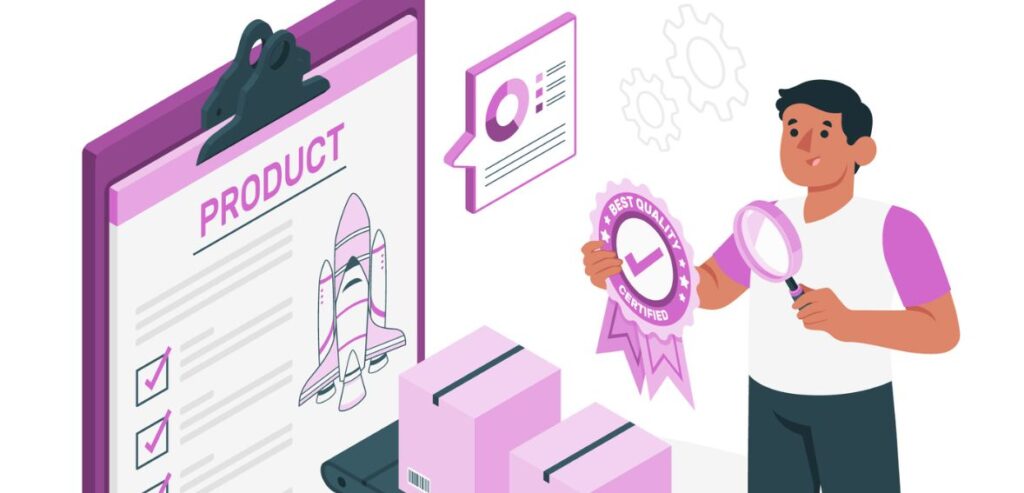
Labels are critical point of contact for both FDA inspectors and customers. Bold claims like “antibacterial,” “kills 99.9% of germs,” or “hospital-grade” aren’t just marketing phrases—they require real, peer-reviewed data to back them up and must align with FDA dosage standards or be approved through formal channels.
The FDA is also stepping up its enforcement of misleading or vague language. Terms such as “all-natural” or “chemical-free” can mislead consumers if not clearly defined and supported by science. Companies will be subject to more scrutiny in 2025 regarding sustainability claims, such as “plant-based” alcohol, and will either have to provide verifiable proof or agree to have unsupported marketing terms removed. When referencing certificates, CoAs, or third-party testing results, QR codes or website references are encouraged, but they must be visible and simple to find.
Sanitizers sold in multi-use bottles larger than one ounce must have child-resistant caps because they can be accidentally swallowed. Additionally, the FDA enforces labeling guidelines for first aid, such as warning that alcohol-based hand sanitizer should not be used in place of soap and water and should not be placed in the eyes.
Regulatory Pathways for New Formulations
Looking for a cutting-edge update, like a foaming sanitizer, non-alcoholic antimicrobial blend, or integrated skin care ingredient? You must have an ANDA or NDA that is backed by safety trials, stability testing, and clinical data. By 2025, the FDA will mandate that the majority of new sanitizer applications contain:
- Comparative efficacy studies against monograph standards
- Human dermal tolerability data to rule out irritation or allergy
- Stability data spanning at least 24 months, with condition-based degradation thresholds
- Environmental and microbiological assessments to ensure consistency throughout shelf life
New excipient ingredients must have Generally Recognized As Safe (GRAS) status or analogous approval, and any intellectual property related to formulations must be disclosed. Innovative labeling (like for “probiotic-infused” products) may be scrutinized to confirm they don’t mislead consumers regarding antimicrobial action.
Importing Hand Sanitizers and Supply Chain Controls
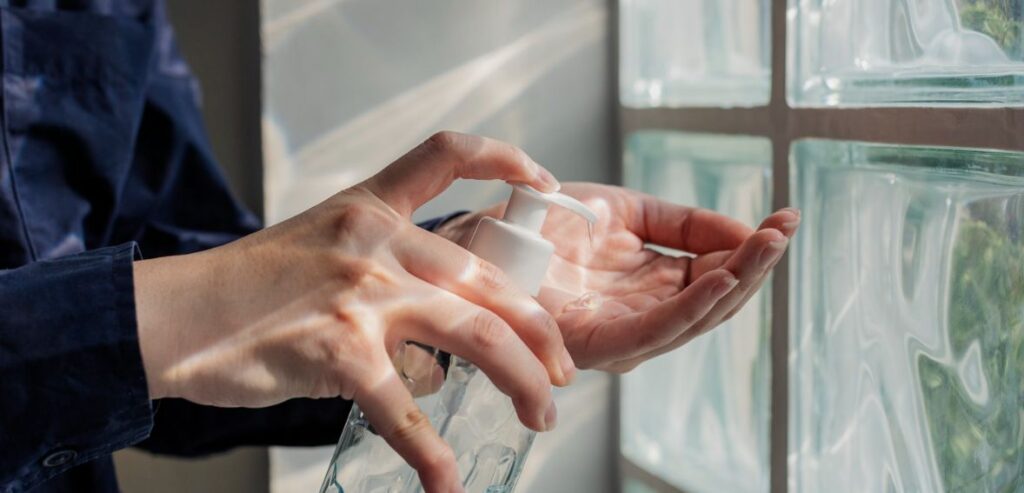
Because the ingredients in hand sanitizer frequently travel across international borders, supply chains need to be open and transparent. The FDA anticipates that importers will verify foreign suppliers by 2025, and they will need to submit audit results, certifications, and certificates of authenticity. International alcohol origins require U.S.-based Quality Agreements with raw ingredient suppliers.
From drums to bulk tankers, shipping and storage conditions are closely examined, particularly for combustible substances like ethanol. Any hand sanitizer or ingredient coming from nations with a history of methanol contamination or with weak regulatory frameworks is screened by port of entry inspections. Batches with inconsistent labeling, mismatched documentation, or CoAs from unidentified labs are seized by U.S. Customs. Retaining shipping records and transport temperature data is highly recommended for manufacturers.
Emergency Preparedness and Stockpiling Obligations
The early pandemic revealed weaknesses in the supply of hand sanitizer. The FDA established business-continuity guidelines in 2025, requesting that producers prepare for spikes in demand, whether due to disease outbreaks, natural disasters, or geopolitical events that affect the production of alcohol.
According to these recommendations, sanitation manufacturers should keep a minimum of one month’s supply of essential components or completed goods on hand. Governments can reserve capacity in times of emergency by entering into public-private agreements. In order to help the FDA anticipate shortages and coordinate with federal stockpiling efforts, medium- to large-scale manufacturers are asked to provide the agency with production forecasts.
Consumer Guidance: What to Look For in a Safe Sanitizer
Although the majority of the work is done by government oversight, consumers can also make more informed decisions. Products should have at least 60% ethyl alcohol or 70% isopropyl listed on the label. Steer clear of sanitizers that seem hazy, smell strange, or have claims that seem too good, such as “no alcohol formula” or “kills 100% of germs.”
Test results or recall notifications can be found by scanning QR codes or visiting manufacturer websites. When in doubt, choose well-known brands, trusted sanitizer retailers, or neighborhood pharmacies that carry FDA-approved goods. Lastly, always adhere to the directions: use paper towels to open public doors after using sanitizer, as its effectiveness diminishes after drying, and apply enough sanitizer to remain wet for at least 20 seconds.
Looking Ahead: What’s Next in FDA Sanitizer Policy
Regulations will change as consumer expectations, environmental safety, and microbial resistance do. According to reports, the FDA is investigating standards for “biodegradable” or “environment-friendly” sanitizers and evaluating substitute antimicrobials, such as benzalkonium chloride, ingredient by ingredient. Future revisions might also mandate recycled packaging or more stringent disclosures of carbon footprints.
Some new technologies, such as UV-light synergistic devices, self-sanitizing dispensers, or smart sanitizers that monitor usage, will probably need more investigation. Anticipate new over-the-counter medication uses and a complex regulatory framework involving health and environmental agencies. Companies implementing this next generation of sanitizer technology will need to be transparent and cooperative.
Conclusion
Although the idea behind hand sanitizers may seem straightforward, by 2025, the FDA’s regulatory structure had changed significantly. Global supply dynamics, consumer protection, and public health all intersect with these products.
Every bottle must be worthy of being placed on store shelves, from stringent manufacturing procedures and formulation standards to strong labeling regulations and new emergency preparedness guidelines. This rigor benefits consumers by giving them confidence that sanitizers are transparent, safe, and effective.
However, that trust also entails accountability. Whether you work as a chemist, manufacturer, or sanitizer user, keeping up with FDA regulations guarantees that you’re contributing to the protection of public health. The best approach, as regulations continue to change, is one that is based on diligence, adherence, and a dedication to quality—because when it comes to health, there is no margin for compromise.